Lightweight, compact, high-precision aluminum die casting
Precision Aluminum Casting
Aluminum die casting
For reducing the occurrence of defective products, we have developed a unique manufacturing method We are perform CAE analysis as developed from our clutch manufacturing technology. We are working on high quality, lighter weight, shorter delivery period, and cost reductions.
In addition, since the casting process is susceptible to temperature, humidity, and other factors, we will establish a factory and aim to create a high-efficiency, high-precision production environment by fully utilizing IoT and AI.

Small cutting tool allowing deep groove machining
Material:SKD61(HRC46)
Equipment:YASDA YBM950V
Insert:R0.5×30×30’
Cutting to mirror finish
Material:SKD11(HRC58)
Equipment:YASDA Vi40
Insert:CBN+PCD
面粗度:Ra0.02
Solid quality assurance through integrated in-house production
We organize an integrated system where all processes from Design (Short LT by 3D design) → Analysis (actual error less than 10%) → Manufacturing (high-precision processing) → Measurement (high-precision measurement) → TRY (accumulate casting data and implement AI analyses) → Analysis (pursuit of true cause and feedback) are all performed in-house.
High Analytical Capability for Zero Defects
Improved correlation between each analysis of flow, solidification, and deformation simulations. In addition, highly accurate analysis realizes a real deviation of less than 10%.
The measurement of internal casting cavities using a CT scanner and the observation of microstructures using a scanning electron microscope are also implemented with a target of zero defects by enabling efficient quality improvements.
Flow Analysis
Solidification Analysis
Tooling Deformation Analysis
Tooling Stress Analysis
Die Casting Technology to Create Thin-Wall Casting
Produce aluminum thin-wall castings by using CAE analysis and die temperature control technology. We have achieved a minimum wall thickness limit of 0.6 mm. With a draft angle of 0° we are able to produce a lighter weight, space saving, and reduced cost casting.
Unique Manufacturing Method Cultivated in Clutch Manufacturing
The local pressurization method that specifies the amount of indentation based on FCC's unique calculation method and the center gate method that takes advantage of the characteristics of directional solidification can meet the high quality and precision requirements for large deep and thick-wall components.
SINGLE CLUTCH
TRIPLE CLUTCH
Combination With Papermaking and Bonding Technologies
Provision of Value-Added Aluminum Products
FCC specializes in multi-disciplinary capabilities to integrate papermaking, joining, and cast aluminum technologies to provide unprecedented, high value-added products.
Overseas Production
With Locations in, Asia, North America and China, FCC has a global reach.
We possess the same production facilities and development technologies in our overseas plants as we do in Japan, which makes it possible to supply high-quality products to the local supply chain in a timely manner.
High Pressure Casting
With high-speed, high-pressure injection of molten metal, this method is excellent for thin-walled castings and offers a shorter cycle time and high productivity.
DISTRIBUTOR
- Equipment Wt
- 350t
- Material
- ADC12
- Process
- HPDC + Slide
HOUSING (Single Clutch)
- Equipment Wt
- 350t
- Material
- ADC10 equivalent
- Process
- HPDC+HPDC + Local Pressurizing (squeezing)
HOUSING (Triple Clutch)
- Equipment Wt
- 800t
- Material
- ADC10 equivalent
- Process
- HPDC + Center Gate
We develop aluminum products applicable to next-generation automobiles, as well as OA equipment, home appliances, and structural members for architecture.
With the increasing demand for electrification, we developed thin-wall precision aluminum die-cast products such as the heat sinks focusing on cooling efficiency with the emphasis on lightweight, thermal management, and EMC countermeasures.
Development of Thin Wall Die Cast Products
Developed for both lighter weight and enhanced cooling efficiency.
The honeycomb structure with high strength is achieved. The height of the honeycomb is 10 mm and the case thickness is 0.6 mm representing our thinnest cast wall resulting in a draft angle of 0° on the inner and outer walls of the case.
The high thermal conductivity alloy HT-1 used for casting is ideal for components that require heat dissipation characteristics, such as computers and game consoles. It has one of the best levels of fluidity among die-casting alloys, allowing the hot metal to circulate even in thin-walled zones.

- Material
- HT-1
- Size
- W142 x D140 x H160 mm Honeycomb Height 10 mm
Advantages of Thin-Wall Die Cast Products
Lightweight
Enhanced Cooling Efficiency
Shortened heat transfer time and increased surface area
Combined capabilities with core technologies (radio wave absorbing paper, etc.)
Pin-Type Water-Cooled Heat Sink
Developed as a die casting product aimed at improving cooling efficiency.
Based on flow analysis simulations, a unique gate design can be established. By forming a pin shape providing a larger surface area, we are capable of a highly efficient product with a high degree of design flexibility suited for complex waterways.
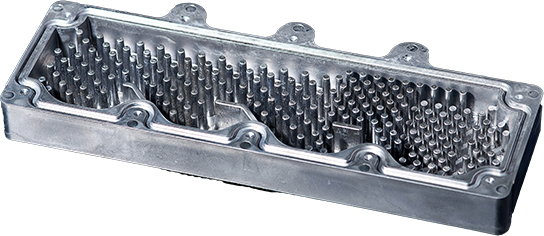
- Material
- ADC12
- Size
- W210 x D60 x H20 mm
Pin Diameter: Tip φ2.9 to φ3.2
Advantages of Pin-Type Water-Cooled Heat Sink Products
Enhanced cooling efficiency
Increased surface area by pin shape
High flexibility of design
Allocation in a tight space
Combined capabilities with core technologies (radio wave absorbing paper, etc.)
- Structural Components for battery modules
- Provision of lightweight, high-strength products by applying the honeycomb shape as a structural component of cases for batteries, inverters, and other devices.
- Exchangeable lithium-ion battery case
- Application as an exchangeable lithium-ion battery can contribute to the improved strength of crushable zones while featuring the lightweight due to thinner wall thickness that can also contribute to the reduced number of parts in the product through manufacturing an integrated piece.
- Compact ECU case
- Application to ECU and PCU cases contributes to enhanced heat dissipation and electromagnetic shielding performance, as well as to a reduced number of parts in products through the lightweight feature and manufacturing in an integrated piece.